Mechanical installation
works
Compressed Air Installations
Compressed air can be thought of as a fluid in which energy is accumulated. Energy in another form is first transferred from the driving machine (electric motor, explosion engine, turbine, etc.) to the compressor in the form of mechanical energy, and in this "work machine", the internal energy of the fluid is transformed into the form of potential energy or pressure energy. Later, this energy is used for various purposes, including transmitting air to distant points and obtaining mechanical energy from the pressure potential.
During all these transformations, it constantly encounters "irreversibility" losses and a series of efficiency concepts emerge. The topics will be discussed later in the order specified in the special section.
PRODUCTION OF COMPRESSED AIR
COMPRESSORS
Work machines that take the atmospheric air and compress it are called air compressors. They can be classified in various ways. The 1st diagram shows the classification given in ISO 5390-1977. Today, compressed air compressors can be classified differently for industrial use. The second scheme is handled from this aspect.
The two most characteristic dimensions for compressors are the operating pressure range and the free air flow rate. This flow rate is the flow rate that the compressed air will have when it is brought to the suction conditions. According to PNEUROP standards (5), standard suction conditions are 20 °C, 1 bar. Nm3 (Normal m3) used in physics is the volume determined at 0°C 760 Torr conditions.
Pressure Units:
Pressure measurement units are increasingly specified in the art in accordance with the ISO measurement system.
However, since old catalogs and measuring instruments are still used today, they are compared in Table 1.
Compressor Room:
Major installation elements in compressor rooms where compressed air is obtained, stored and prepared:
- Compressor unit (complete with air suction filter, inter- and after-coolers, oil coolers and separators, safety valve, no-load lift, capacity control and safety organs, drive motor, and all other elements)
Additional compressed air aftercooler and water separators
Compressed air tanks
Compressed air (oil) filters
Compressed air dryers
Connection pipes and valves
Oily condensate water system
The compressor room, where the compressed air is obtained, should be an airy, easily opened volume with a solid floor. In industries such as Cement-Textiles, where the atmosphere is very dusty and volatile fiber, and in dusty areas, compressor rooms should be fully closed and ventilation systems that give filtered air inside should be foreseen. In some cases, the compressor suction can be extended with a suction pipe towards a less dusty environment and the compressor air suction filter can be placed here. While sizing the suction pipe, care should be taken to keep the suction losses below 50 mbar.
In the ventilation of the compressor room, care should be taken to remove the part that passes from the energy converted into heat in this volume to the ambient air. Otherwise, unacceptable temperature rises occur in the compressor room. In practical calculation it can be assumed that all the energy used by the compressor drive motor is converted to heat. When the part taken with other fluids (cooling water, compressed air used in the installation) is removed from this energy, the amount of heat that needs to be removed by ventilation can be found.
In air-cooled compressors, fans driven directly from the drive motor shaft or on the compressor main shaft blow the cooling air onto the compressor cylinders or intercoolers. There are also fans driven by a separate electric motor. Complementing the cooling function
hot air should not be directed over another compressor or air-cooled compressed air dryer of the same volume. It is best to blow this air directly outside or towards the exhaust air hood.
The two most important external factors that affect the air delivery efficiency of the compressed air compressor are the temperature of the sucked air (0 compressor room temperature) and the pressure losses in the suction. In this regard, it is of great importance that the air intake filter is sized appropriately. Figure 1 shows the layout of a compressed air compressor room.
Compressor Intake Air Quality:
Since the compressed air is obtained from the atmosphere, the gas, aerosol, vapor mixed with the atmosphere in any way, as well as the solid particles that can pass through the suction filter, pass through the compressor with the air and carry oil and coked oil particles from the compressor cylinder and valve surfaces into the compressed air. For example, particles in the form of microscopic fibers in the poorly filtered compressed air in textile factories can create special problems at some points of use. The more dust-free the intake air is, the less frequent the compressor failures, and the longer the life of the oil, separator and filters. In this respect, maximum attention should be paid to the cleanliness of the compressor room air and the efficiency of the compressor suction filter.
Pressure Levels:
Compressed air networks installed in factories and private buildings are generally foreseen at pressure values such as 7-10-16 bar. Compressed air may be needed at two different pressure levels in a business. Depending on the amount of compressed air required at each level, two separate independent installations can be installed. If the required air flow at the low pressure is relatively low, it can be supplied to the low pressure circuit by reducing the air pressure through a regulator from the high pressure circuit.
General Compressor Constructions:
Today, oil-injected screw compressors, which are more advantageous in terms of ease of maintenance and operational safety, are increasingly replacing reciprocating compressors. (Picture 1-6)
Oil-injected screw compressors can be made as single-stage up to 13 bar pressure. Because the oil injected between the screws by the suction ensures that the outlet temperature is kept around 80-100°C. On the other hand, in oil-free screw compressors, the compression is not isentropic and the temperature rise of the compressed air is higher than the other. In these compressors, the compression ratio in one stage should not exceed 3.5. In this regard, in practice, single stage up to 3.2 bar, 2 stages up to 10 bar and 3 stages above that are designed. There are intercoolers between the stages.
Small reciprocating compressors are designed with a single stage up to 8 bar, and more stages above that. In medium capacity (2-6 m3/min free air) reciprocating compressors, the compression ratio in one stage should not exceed 3.5.
Compressor Units:
Small and medium sized compressors can be supplied as a compact unit with a compressed air tank and other accessories preceding it in the system. (Picture 10-12) In recent years, some companies have added compressed air dryers and oil filters to the unit.
Noise Issue:
Since the noise produced by air compressors is a kind of environmental pollution, it must be isolated. Compressor units can be placed in silent cabins, except for the precautions to be taken to prevent the noise from being reflected outside in the compressor rooms. Thus, the noise level can be reduced by 10-15 dB.
Capacity Control of Compressed Air Compressors:
Capacity control is done according to the network pressure.
Piston Compressors:
In small types, on-off control is performed. The pressure range is at least l bar and can go up to 3-4 bar. This shape is applied in small workshops and places of use. Since frequent stop-starts are undesirable for the electric motor in compressors with large motors, capacity control is performed in the form of load-idle operation. In electric motor types, the compressor suction valves are kept open with a pneumatic control mechanism, so air does not blow even though the compressor is driven. Another method applied in reciprocating compressors driven by blast motors is the use of centrifugal or magnetic clutches. Although the engine is running continuously, it works during the times when the clutches are engaged with the control.
Screw Compressors:
The normal pressure range in the stop-start control with idle time control is 1 - 2 bar. In networks where pressure fluctuations are not desired, the pressure range is 0.5 bar. In large screw compressors (P motor 37 kW), it is possible to control the capacity with a proportional control system so that the mains pressure remains constant. Various solutions should be compared in terms of energy savings to be achieved.
Oil Coolers:
Oil coolers of lubricated screw compressors can be air or water cooled. Since most of the energy consumed for compression is transferred to the oil, it is possible to benefit from this heat at a temperature of about 50 - 80°C.
STORAGE OF COMPRESSED AIR
Compressed Air Tanks:
Compressed air tanks can be vertical or horizontal cylindrical shape. These tanks are manufactured and tested according to TS 1203 standard in our country. There are hand or man hole, air inlet - outlet, water discharge, safety valve, manometer connection ports on the tank. The tanks are delivered with a test certificate and are subjected to a pressure test for a period of one year. Compressed air tanks can be placed inside the compressor room or in the open air. In Table 2, a size chart of vertical compressed air tanks, the main dimensions of which are determined according to the minimum waste in the sheet metal cutting, is given.
PREPARATION OF COMPRESSED AIR Additional Aftercoolers:
When the aftercoolers of screw compressors, which are designed especially for the conditions of cold regions, are insufficient, additional aftercoolers are installed. Apart from this, some compressor designs are given separately after coolers. In parallel with compressor cooling, compressed air aftercoolers can also be air or water cooled. (Picture 13-14) The condensed water as a result of cooling is separated from the air in the water separator by dragging some of the oil in the form of aerosol vapor that may be present in the compressed air. (See table in Appendix 3) This water is discharged from the separator with the help of an automatic draining device with a float or solenoid valve. Air-cooled aftercoolers can contribute to the ventilation of the room, if optimally placed in a window in the wall of the compressor room. The outlet temperature of the compressed air from the water-cooled aftercoolers is approximately 5°C above the water inlet temperature. In air-cooled aftercoolers, this value is 10 - 20°C above the cooling air temperature.
Compressed Air Dryers:
Condensed water in the sections where the compressed air temperature drops may cause malfunctions due to corrosion in the installation. In this respect, before being supplied to the pipe network, which is usually made of steel, the moisture in the compressed air must be separated from the air at a level that cannot be separated in the advanced parts of the installation. Drying of the air is done by artificially cooling and separating the moisture or passing it through a hygroscopic material. Accordingly, in principle, there are two types of compressed air dryers:
Refrigerated and absorption types. Of these, the cooled ones can reduce the dew point of the air to at least + 2°C, and the ones with absorption up to 70°C. (Picture 15-16)
Compressed Air (Oil) Filters:
There is oil in the range of 3-50 ppm, depending on the type and condition of the compressor, in the air coming from the lubricated type air compressors. Oil and other solid particles create major quality and operational problems for many users such as paint, pneumatic control instruments. For this reason, compressed air must be filtered. Compressed air filters are foreseen in all installations made recently. In cases where oil is not important, filters with sinter - metal elements filtering particles larger than 20 -30 μm are used. Compressed air filters, which filter particles up to 0.1 μm in size with the oil in the compressed air, are divided into two stages as preliminary and precision. Pre-filters can filter oil generally up to 1 mg/m3 and precision filters up to 0.01 mg/m3. (Picture 17) Compressed air degreased by passing through pre- and precision filters can then be used as breathing air after it is passed through a filter of activated charcoal and dust, and is purified from CO, odor and all solid particles. In Figure 2, the locations of the various compressed air installation elements mentioned above in the installation are indicated in terms of functionality.
TRANSMISSION AND DISTRIBUTION OF COMPRESSED AIR Connection Pipes And Valves:
In compressed air networks up to 10 bar, galvanized pipes with a diameter of up to 1 /" are preferred, while flanged connections are preferred. Beyond this, flanged connections are used. Welded welded steel pipes can be used easily in networks up to 16 bar in systems with dryers. Diameters up to 2" and 10 Ball valves at pressures up to bar can be used alongside other plumbing valves. Butterfly valves with larger diameters are advantageous in terms of pressure loss.
Transmission and Distribution:
In networks where compressed air dryers are not used, as the temperature of the air flowing into the pipe drops, the water vapor in the air condenses and is dragged along with the air. With the help of water traps to be placed at the critical points of the installation, water can be drained from the lower points. Another precaution that is recommended to be taken in branches is to make the branch outlet from the top.
Pipe distribution networks can be made in the form of forks, fishbones and rings. If there are users using sudden high flow near the end points, end compressed air tanks can be installed here. Thus, velocity and pressure fluctuations in pipes can be reduced. (Figure 3)
Connecting End Users:
Quick connect couplings and hoses: Hose connection is preferred between the branch end and the user to accommodate minor user displacements. Special quick-connect couplings provide speed in disconnecting and connecting the user equipment. (Figure 4-5)
CONDITIONING OF COMPRESSED AIR
Some compressed air end users require air of a different quality from the mains air. These can be grouped into 4 categories.
Regarding the Moisture Content of the Air:
Especially in systems that do not have a compressed air dryer, a water trap or compressed air dryer is placed just before the user to obtain compressed air with the special dryness desired by this user. In some networks, there is a refrigerated type compressed air dryer in the compressor room, while the user may need drier air. In this case, an absorption compressed air dryer can be placed at the head of this branch. The capacity of this dryer is enough to meet the requirement in the branch.
In terms of the Particulate Content of the Air :
Special compressed air filters that differ from previous filters can be used.
In terms of Oil Content of the Air :
Lubrication of air-using systems such as compressed air cylinders, compressed air motors and hand tools is provided by oil dosed to the air in compressed air pipeline lubricants.
Humidification of the Air:
Humidifiers that give moisture into the dry air are used in operating room breathing air applications. They generally work on the hookah principle.
Oily Condensate Water Installation
The direct discharge of oily condensate, which is separated from the air in the intercooler, aftercooler water separators, compressed air tank, filter and compressed air dryer of the oily compressor, to the sewer or to the ground brings a large polluting load to the environment. To prevent this, oil-water separators are used. The easiest way is to use separators operating on the static-gravity-stratification principle. The oils separated from the condensate water are collected in a separate container and delivered to the collection points for reuse.
DIMENSIONING OF COMPRESSED AIR INSTALLATION
DETERMINATION OF COMPRESSOR CAPACITY
After making a list of compressed air users, the consumptions and operating periods of each of them are determined. Today, there are various areas where compressed air is used, from printing to the textile industry, from packaging machines to special assembly stations, from plastic machines to paint shops. In the catalogs of special machines, the desired air properties and consumption in terms of free air are specified. For (old) machines where this is not specified, consumption can be found with a simple operating test. While the machines are running, their simultaneity status should be learned from the business expert.
Calculation of the compressed air flow rate to be used in compressed air facilities with various purposes and many users has to be based on some estimates. Here, if possible, the total compressed air consumption in a shift can be calculated based on the production procedures and figures (daily / hourly actual working time x average air consumption value of each pneumatic tool or machine using air). The air consumption of air tools is given in Table 3 (9). In Table 4, the air usage spreadsheet of an enterprise is given as an example (7).
In enterprises where compressed air is used for production purposes in the 1st degree, sufficient safety must be foreseen in the compressor capacity. In the table below, the minimum reserve percentage that should be according to the number of compressors that meet all consumption is given.
Beyond that, it is not recommended to operate the air-cooled, workshop type reciprocating compressors continuously for 24 hours. For maintenance and oil cooling, the capacities of these compressors should be chosen with a tolerance of 25% -50%.
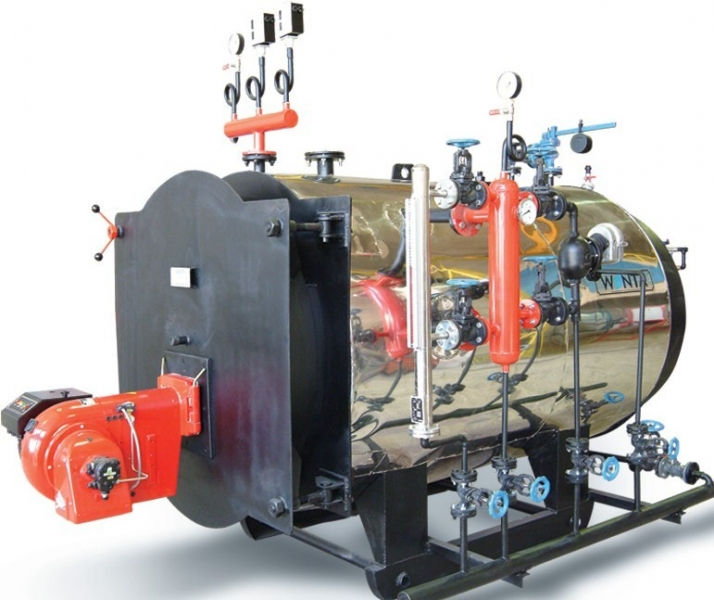


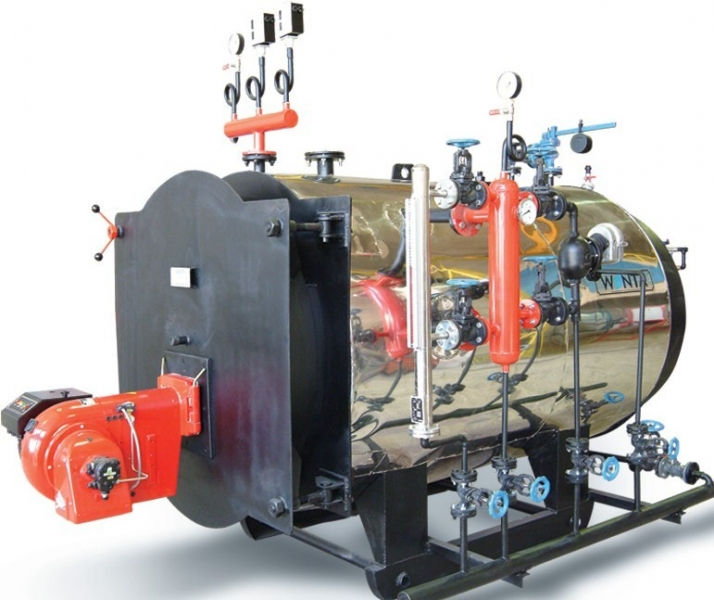
Hot Oil Installation
Considerations in the Construction of Hot Oil Installation
1.Thermal Oil Expansion Tank: It should be at least 30% of the total thermal oil volume in the installation (including the boiler). The diameter of the expansion tank should be as small as possible (so that the surface in contact with the atmosphere is small) and the tank should be placed in a vertical cylindrical shape.
2. Reserved Oil Tank: It should be at least 1.5 times the volume of all thermal oil in the installation.
3.Thermal Oil Circulation Pumps: They should be specially designed for high temperatures, preferably air-cooled, cast steel or ductile iron.
4.Thermal Oil Filling Pumps: Gear pumps designed according to the viscosity of the thermal oil at room temperature can be used.
5. Valves, Check Valves, 3-Way Valves: They should be resistant to the operating temperature of thermal oil, copper or copper alloys should not be used in their internal parts. Valves should be PN16 ductile iron or PN25/40 steel casting.
6.Filters: They hold the solid materials carried with the oil in the installation. They need to be cleaned from time to time. It is appropriate to choose the filter surfaces as large as possible in terms of reducing the frequency of cleaning. A manometer must be connected to the filter inlet and outlet in order to be able to see and intervene in the resistance that will occur due to the contamination of the filter.
7.Thermal Oil Level Indicator: It should be in accordance with the temperature and characteristics of the thermal oil in the expansion tank.
8.Pipe Installation and Fittings: All pipe fittings must be steel. It is allowed to use unalloyed steels below 300 °C. In piping carbon (for example ASTM A-53 and ASTM A-106) or St. 35.8 Seamless steel drawn tubing can be used. Cast iron is never used in hot oil installations. (Due to the danger of breakage, cracking, oil leakage) The piping should be properly inclined and an air discharge pipe and valve should be placed in places where there is a possibility of air collection. Pipes circulating oil should be insulated with rockwool in sufficient thickness.
9. Instruments: The following instruments must be present in the hot oil system for safety and control.
a. Burner control thermostat
b.Maximum temperature thermostat
c.Differential pressure switch or flow switch stops the burner when the oil circulation slows down or the oil circulation pump fails.
d.Expansion tank minimum oil level lock, when the oil level falls below a certain level, it turns off the burner by giving an alarm.
e.Chimney thermostat: When the oil circulation is stopped for any reason: it deactivates the burner as the flue gas temperature will rise.
10.Thermal Oil to be Used in the System: Made from mineral oils; Mineral oils that do not lose their properties at high temperatures, do not have corrosive properties, and do not deteriorate their thermal stability (heat transport properties) should be preferred.
11.Expansion Tank: It is the only place where the thermal oil in the system comes into contact with the air. In order to avoid oxidation, the temperature of the oil in the tank should not exceed 60 °C. The facility should be constructed in such a way as to guarantee this condition. To reduce the air-contacting surface of the oil in the tank; The expansion tank should be manufactured as a vertical cylindrical tank and mounted at a higher point than the highest point of the installation so that it will not cause a problem for the circulation pump to be pumped outside the building. The expansion tank must not be insulated. (However, it can be taken into a closed area in places where there is a danger of frost.) The connection of the installation with the expansion tank is provided before the suction of the circulation pump and with a 1 1/2" - 2" diameter non-insulated pipe.
12.Thermal Oil Storage Reserve Tank: Put the reserve tank at a depth where all the oil in the installation will be discharged with natural flow. If possible, put a level gauge or petrometer on it. Start to fill the oil system with a hand pump or gear pump from the lowest point. Place an air evacuation system in places where there is a possibility of holding air in the system and ensure that these are open during the oil filling process.
13. Pipe Elongation: The expansions that may occur in the pipes in the hot oil installation due to high temperatures should be taken into account. These elongations become even more important in the connections of installation elements such as boilers and valves. The elasticity of small diameter pipes can sometimes compensate for these elongations. However, in large diameter pipes and especially if there are excess fixtures on the pipeline, compensators should be used at certain intervals and the pipes should be fixed at appropriate places.
14.Air Evacuation System: Precautions should be taken to evacuate the steam and gas collected at the highest points of the system.
15. Blowdown : In order to discharge all the oil and other substances in the installation, a suitable place must be installed.
16. Hot Oil Boiler Rooms: They must be separate from the main building, independent and built on the ground. It should have an emergency exit door (made of fire resistant material) other than the entrance door.
17. Ventilation: There must be a lower air inlet and an upper polluted air outlet, which will provide more air circulation than the combustion air in the boiler room.
Hot Oil System Commissioning Procedure
1.Pressure Test: The hot oil boiler and the whole installation must be subjected to a pressure test with thermal oil or air at a pressure of at least 6 bar. If the pressure test is performed with air, the air must be completely evacuated at the end of the test process.
2.Thermal Oil Filling: In order to prevent air trapping in the installation, thermal oil is started to be pumped into the system by means of the filling pump (gear pump) from the lowest point of the installation. At this time, the air release valves are open. The valves are closed when the air evacuation ends and the oil starts to come out. The thermal oil expansion tank is filled up to 1/3 (minimum level). The circulation pump is operated for 4 hours with the oil cold and the air that may occur in the system is evacuated.
3. Commissioning: The temperature rise rate is increased to 40 C/hour until the thermal oil temperature reaches 90 C. Temperature rise between 90 C and 120 C should not be more than 10-15 C/hour. After that, the system is operated for 6 hours at normal operating temperature. The system is cooled. Foreign materials accumulated in the filters are cleaned.
4.Thermal Oil Test: Periodically check the oil in the system by taking samples as follows. If it has reached the point of replacement, change the thermal oil.
a.The first test is done after the first start-up.
b. The second control should be done after 100 working hours or at the end of the second month.
c. The third and fourth checks should be checked after 2000 operating hours or every 6 months.
d. All subsequent checks should be carried out regularly every 3000 working hours or every year.
5. How to Do the Thermal Oil Test: Oil intake is done in a transparent container of not less than 1 kg and when the system is cold. When the system is cold, the circulation pump is started and stopped for 10-15 minutes and a sample is taken after some oil is poured from the sampling valve in the return line. In the first test (after the first start-up), it is checked whether the thermal oil in the sample cup is clean. If contamination is detected, the oil in the system is drained, filtered and refilled. In the test of the oil in the system, signs of contamination, oxidation and deterioration are sought.
6. Signs of Thermal Oil Deterioration
a. Contamination: residues in the sample thermal oil taken from the installation reduce the thermal stability, heat carrying capacity and heat transfer capability of the oil. In addition, foreign objects such as welding spatter may cause damage to installation elements such as circulation pumps and valves.
b.Oxidation: When the thermal oil temperature exceeds 60 C, it will oxidize if it comes into contact with air. Its viscosity increases. Its fluidity and heat transfer capacity are reduced.
c. Thermal Deterioration: When the thermal oil overheats in the boiler and its temperature exceeds 350-400 C (the general reason for this may be that the oil speed in the boiler stops or slows down) it starts to deteriorate. (cracking). It is seen as black dots (pitching) in the fat. This deterioration may cause the fluid to thicken, decrease its flow ability, increase the resistance in the oil circuit in the system, prevent heat transfer by plastering on the boiler heating surfaces at a higher level, heat accumulation in these areas and fire as a result of punctures. Heavily contaminated and thermal oil must be replaced immediately.