Mechanical installation
works
Steam Installation
Steam is a heat transfer fluid with very good properties, which is widely used in industry and power generation today as it was in the past. Steam installation is very complex compared to hot water, boiling water or thermal oil. It requires knowledge and care in construction and operation. Steam is a widely used fluid for various purposes.
The main usage areas of steam;
Industrial,
Heating,
Electricity generation in thermal power plants
The use of steam for heating only is now abandoned. However, steam is used for heating in special cases. The most important of these reasons is the large elevation difference in the heated area. Due to the high static pressure on the boiler, hot or superheated water cannot be used in these cases or becomes uneconomical. Steam is widely used in the food, chemical, petrochemical, textile industries.
Steam Boilers
•:A closed vessel working under pressure and manufactured to give the heat energy formed by releasing the energy in a fuel as heat to a fluid. It is converted into mechanical energy and used in many fields.
• Boilers are very expensive energy generators in terms of initial investment and operating costs. For this reason, a boiler suitable for the purpose should be selected, and due care should be taken in its operation and maintenance.
CLASSIFICATION OF BOILERS
fuel type,
The type of furnace where the fuel is burned,
The type of fluid they produce,
working pressure,
construction style,
manufacturing material,
to water circulation,
to gas circulation
can be classified in many different ways according to
EFFICIENT OPERATION OF BOILERS
While choosing the boiler, it is necessary to know the annual, monthly and daily steam needs of the enterprise and to consider the load situations that may occur in the near future.
By reducing the steam pressure in the boiler, a savings of 1-2% can be achieved on the fuel bill.
Some of these savings are due to the decrease in flue gas temperature and the resulting increase in boiler efficiency. The heat losses from the boiler surface will also decrease somewhat in proportion to the reduction of the pressure.
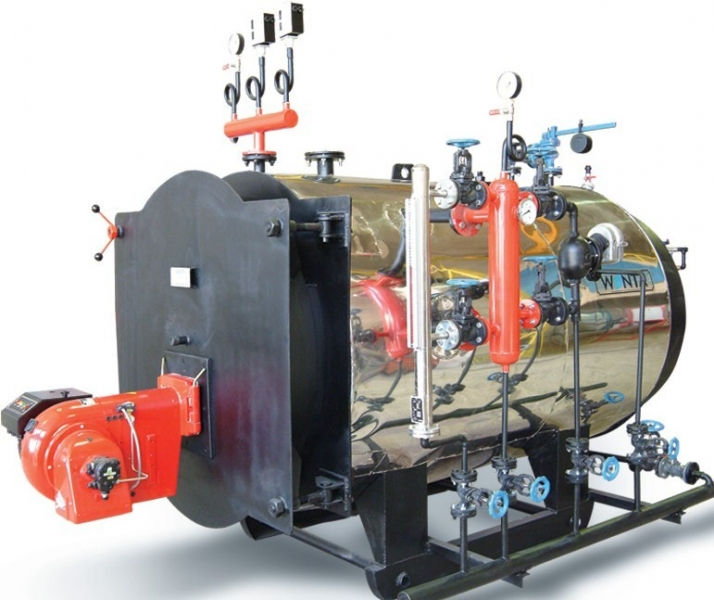

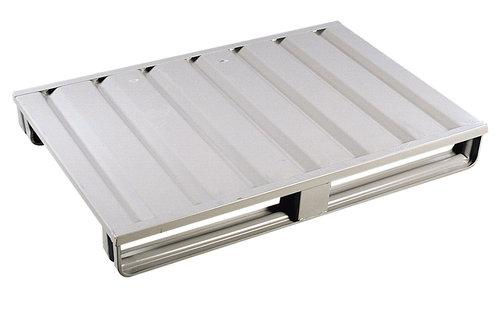
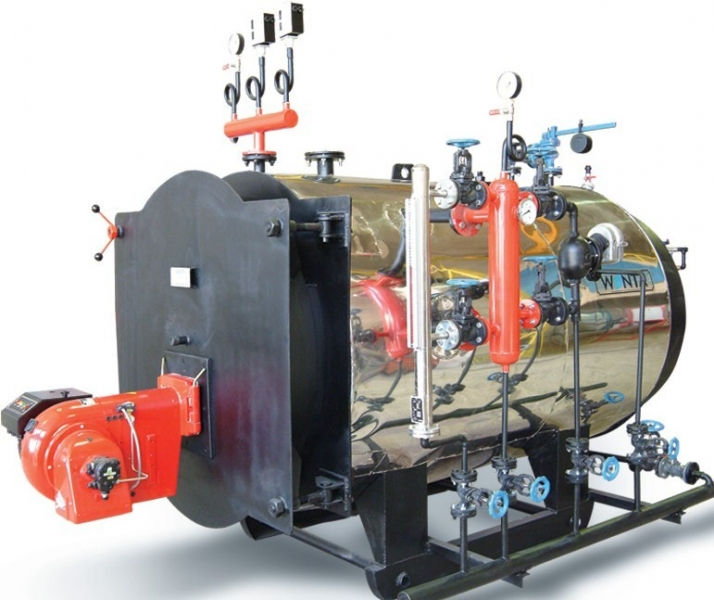
FACTORS AFFECTING BOILER EFFICIENCY
Incomplete combustion (combustion efficiency)
Heat loss due to water vapor in the flue gas
Heat loss due to dry flue gas
Excess air (l)
flue gas temperature
Fuel type
burners
vapor pressure
boiler load
Contamination of heating surfaces
from the boiler surface heat loss
Heat loss due to blowdown
Feed water and combustion air temperature
Boiler and pipe installation external surface insulation quality
Condensate recovery
Incomplete Combustion
It occurs when combustible materials in solid and liquid fuels do not burn and remain in ash or when unburned carbon is formed in the flue gas.
A good combustion can be achieved by adjusting the air excess.
It is necessary to keep the O2 amount in the flue gas at the optimum level. (If the air/fuel ratio is more than necessary, the energy discharged from the chimney will increase)
Flame cooling caused by excess cold combustion air or the passage of the flame through the cold surface also causes incomplete combustion.
Heat loss due to water vapor in the flue gas
The moisture contained in the fuel is released by evaporation after the combustion reaction. This humidity causes some of the useful energy to be thrown out of the chimney. Moisture in fuel possible This loss can be reduced by reducing it as much as possible.
The highest losses with water vapor occur in gaseous fuels due to their chemical composition.